Responding to higher costs with technology
By John T. Ryan
Peru – Customers purchasing apples at Forrence Orchards’ Route 22 packing house over the past few months may have noticed a significant change in its apple packing operations. There’s a new machine in operation; it’s called a sizing machine. The hard-working staff no longer visually examines every apple to determine its grade – Extra Fancy, Fancy, or Utility. Instead, as is the case in almost every industry, computers have entered the process.
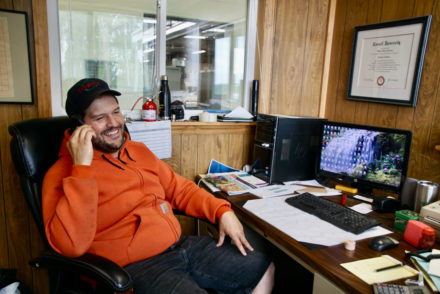
Henry Forrence
Packhouse Manager Henry Forrence explained why the orchard decided to buy the new Tomra-Compac sizer. He stated, “The cost of labor is either fixed or increasing. Today, it’s increasing, so we need to increase our efficiency. The grading is now automated as opposed to having to be done by a human. By automating decision-making, we’ve made every hour worked more efficient. Using our last generation machine our staff had to pick up every apple and decide its grade – Extra Fancy, Fancy or Utility. This machine looks at about 400 different criteria, cameras take 15 pictures of every apple and based on the criteria that I input, it determines the apple’s grade.” Criteria include such factors as size, weight, color, and defects. After grading, the machine directs the apples to the appropriate packing station. All this takes place at between 500 and 650 apples per minute.
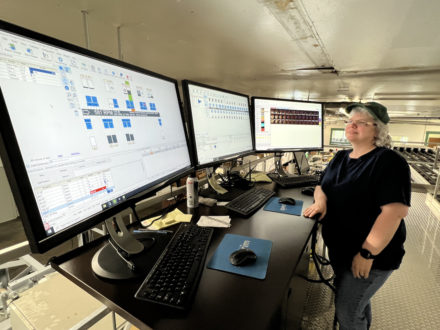
Carolee Furnia
Carolee Furnia, a 27-year Forrence employee, controls the sizing machine from a platform overlooking the packhouse floor. She said, “I’ve been through three generations of machines. This one is a big change.” Each morning Henry Forrence informs Furnia what apple sizes, quantities, and packaging are needed to satisfy Forrence’s customer orders. She enters the information into one of the system’s five computers, monitors three computer screens, and ensures that the job gets done.
Patti Chase, a 22-year packhouse employee, commented as she tied a bag destined for one of America’s best-known chain stores. “I don’t know if I could ever return to the old machine.” Diane Plummer, an eight-year employee working alongside Chase, agreed. Both Chase and Plummer appeared to enjoy and take pride in their essential work.
Forrences were packing their beautiful McIntosh apples when the Peru Gazette visited. Our video traces the apple’s journey into a water flume, where they float onto the packing line. Then, they pass through a succession of machines to be washed, waxed, dried, photographed, graded, weighed, labeled, transported to a packaging station, placed in a bag or tray, boxed, and palletized. Henry Forrence did a quick estimate of the total pounds of apples produced by Peru orchardists each year. It’s a big number – 50 million pounds.
6/23/22 correction – 50 million pounds was incorrectly stated as 20 million pounds.
Posted: June 2nd, 2022 under Adirondack Region News, Agricultural News, Business News, Faces of Peru, Northern NY News, Peru News, Peru resident news/accomplishments, Peru/Regional History.